去年8月本公众号发出“Mini LED,要怎么检?”一文后,得到了很多业内朋友的关注。半年之后,在明锐研发团队的努力下,进一步完善了Mini LED的整线检测方案,增加了锡膏检测SPI及背光点胶AOI,在实际评估与应用中表现优异。因此小编在原推文基础上,更新文章如下,希望对大家有所启发。
如果你关注行业新闻,最近一两年应该经常会看到有关Mini LED的新闻登上“热搜”。正逐渐兴起的Mini LED是什么?Mini LED给工业视觉检测带来的挑战又是什么?今天我们要从明锐的老本行,工业视觉检查的角度,来谈谈Mini LED。
Mini LED是什么?
Mini LED 是「次毫米发光二极管」,指芯片尺寸介于 50~200μm 之间的 LED。由于 Mini LED 尺寸介于传统 LED 与 Micro LED 之间,是在传统 LED 背光基础上的改良版本,目前也算是 Micro LED 发展过程中的最佳替代品。下面这张图,解释了传统LCD、OLED、Mini LED、Micro LED的各自特性。
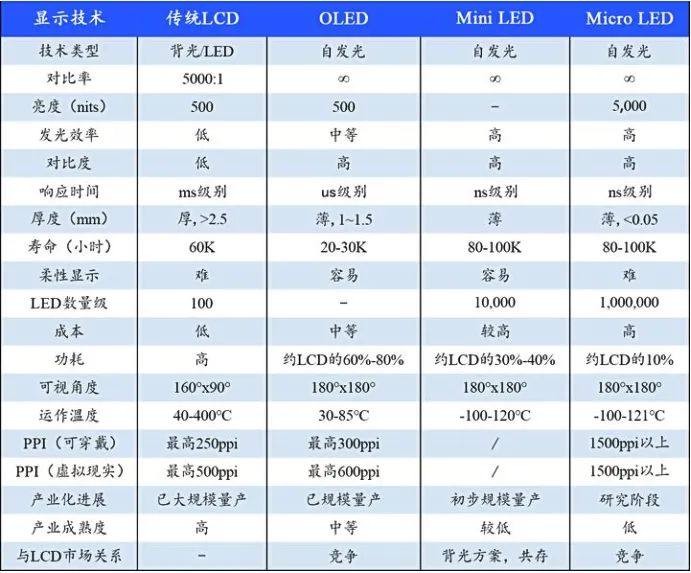
Mini LED有什么优势?
Mini LED 比起传统 LED 来说,颗粒更小、显示效果更加细腻、亮度更高,同时比 OLED 更省电,而且支持精确调光,不会产生 LED 的背光不匀的问题。目前可将 Mini LED 视为 LED 到 Micro LED 之间的过渡,相比于 Micro LED 的低良率,Mini LED 明显在量产方面更有优势,苹果从 2021 年开始在 iPad Pro 和 MacBook 采用了Mini LED。苹果之所以全面转向 Mini LED 面板,主要是 Mini LED 有以下优势:
- 轻薄、省电
- 亮度、对比度均超越HDR(即苹果口中的 XDR)
- 色域更广、颜色更饱和
- 峰值亮度提升 3~5 倍 (>1000nit)
- 显示寿命比 OLED 延长 3~5 倍
- 可比 OLED 省电多达 80%
- 成本比 OLED 更低
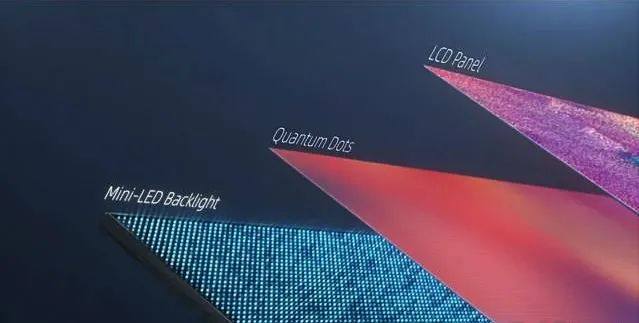
Mini LED的应用及工艺
从应用来看,Mini LED可分为背光和RGB显示两个方向。
1. Mini LED背光技术通常采用蓝色芯片搭配转色材料实现白色背光,再结合液晶面板实现画面显示。Mini LED背光具有局域调光(Local Dimming)技术,能够通过精细分区,对整体画面进行动态调光,从而实现高动态对比度。应用场景包括可穿戴显示设备、电视、车载显示、电竞和笔电显示等。
▼ Mini LED背光产品整板图(未通电)
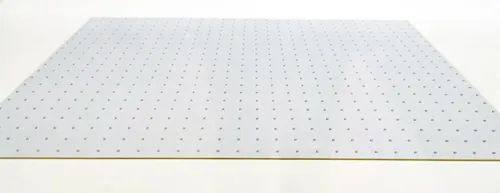
▼ Mini LED背光板产线示意图

2. Mini RGB显示是自发光技术,相当于小间距显示屏的技术升级版,通常是由RGB Mini LED芯片组成显示像素,再通过SMT或COB封装的方式贴在驱动基板上,作为显示屏直接显示,应用场景包括可穿戴显示、高清移动显示、车载显示、高清大尺寸显示等。
▼ Mini RGB直显芯片图
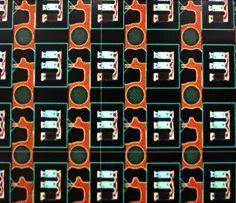
▼ Mini RGB直显板产线示意图

由于技术尚不成熟、成本偏高,Mini RGB显示尚未到达冲刺量产阶段。不过,会议室、指挥监控、高端商业显示、安防等公共服务大尺寸显示的需求正在被激发。
Mini LED如何检?
先做个对比,在我们熟悉的SMT工艺中,目前已量产使用的最小CHIP元件为01005(公制尺寸为400μm*200μm),而Mini LED的颗粒尺寸在50~200μm之间,最小的尺寸为125μm*75μm,大小仅相当于01005CHIP元件的1/9,这要求检测设备的视觉更加精细,AOI镜头要有微米级的分辨率,才足够拍清楚每颗LED芯片的细节。并且,在一块Mini LED板上,最多可达十万颗LED芯片,这不但要求硬件上配置更大像素的相机保证视野面积,以确保检测速度跟上产线速度,而且超大的计算量也是对算法及软件的一个挑战。除了检查Mini LED芯片的错漏反偏等不良,对Mini LED的性能要求,是每颗LED颗粒均能正常发光。这时需要给面板供电,让每颗Mini LED颗粒亮起来,这被称为LED的点亮测试。检查每颗LED颗粒是否正常发光,也是AOI检测不可或缺的环节。
Mini LED给检测设备带来的新挑战,总结如下:
1. 更小的芯片尺寸对分辨率的要求更高
2. 更薄的锡膏厚度对于SPI还原精度的要求更高
3. 更小的芯片尺寸要求更小的偏移检测能力,重复精度要求更高
4. 10万数量级的芯片检测要求电脑硬件和AOI软件具有更快的计算能力
5. 针对大尺寸背光板,要求检测速度更快
6. 针对背光产品透明lens胶的检测,对算法能力要求更高
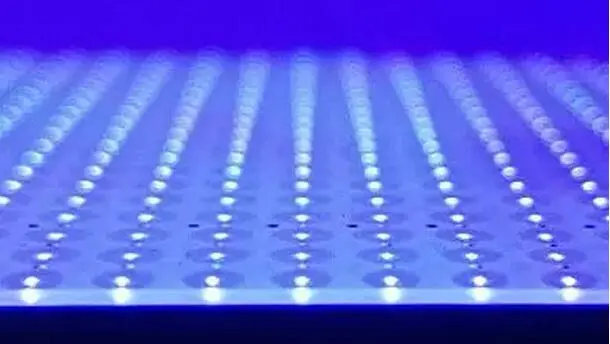
应新的挑战,明锐成立了Mini LED专门项目组,经过一年多的努力,目前已逐一攻破了这些技术难关。
对于Mini LED的锡膏检测,锡膏厚度仅有20-50um,焊盘尺寸仅70-200um,明锐SPI提供了5um分辨率的镜头方案,以满足高精度检测需求,并可支持数量超20万焊盘的检测程序无卡顿,另外锡丝短路算法,可有效拦截Mini LED 超小间距焊盘间的连锡不良。
▼ 明锐SPI镜头下的Mini LED锡膏3D图像
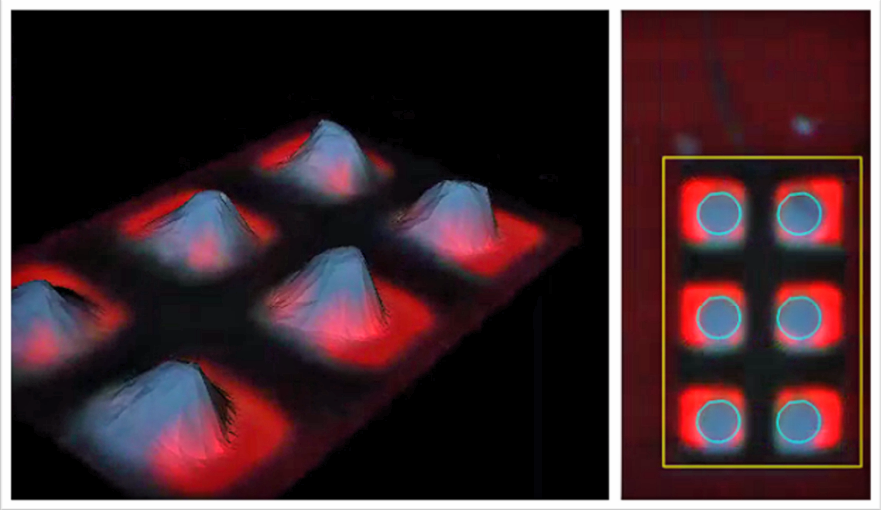
对Mini LED的微小芯片检测要求,明锐AOI提供了不同分辨率的镜头方案,包括2.3μm、3.4μm、4.3μm、6.3μm等,可针对不同的芯片尺寸提供相应的解决方案。另外更高分辨率会导致镜头景深变小,这样可能因板弯变形而出现拍图模糊,明锐AOI为此设计了真空吸平台、Z轴可调等选配功能。同时Mini LED的微小芯片对设备的重复性提出了更高要求,明锐AOI通过升级现有的硬件机械平台,确保机械重复精度达到±10μm以内,配合AOI软件算法的进一步优化,确保其重复性可以达到±1个像素。
在Mini LED背光检测过程中,点胶固化后,由于lens胶呈不规则透明状,对于检测算法能力要求很高,明锐通过特殊的光学处理、高精度的轮廓切割算法,可精确检出lens胶直径与偏心距,与二次元检测的精度误差控制在15μm以内。同时结合AI深度学习算法,针对气泡、褶皱、塌陷、剥离等低对比度的不良进行特征点提取,实现检出。
▼ 明锐AOI镜头下的Mini LED背光炉后图像
(在优化打光参数条件下)
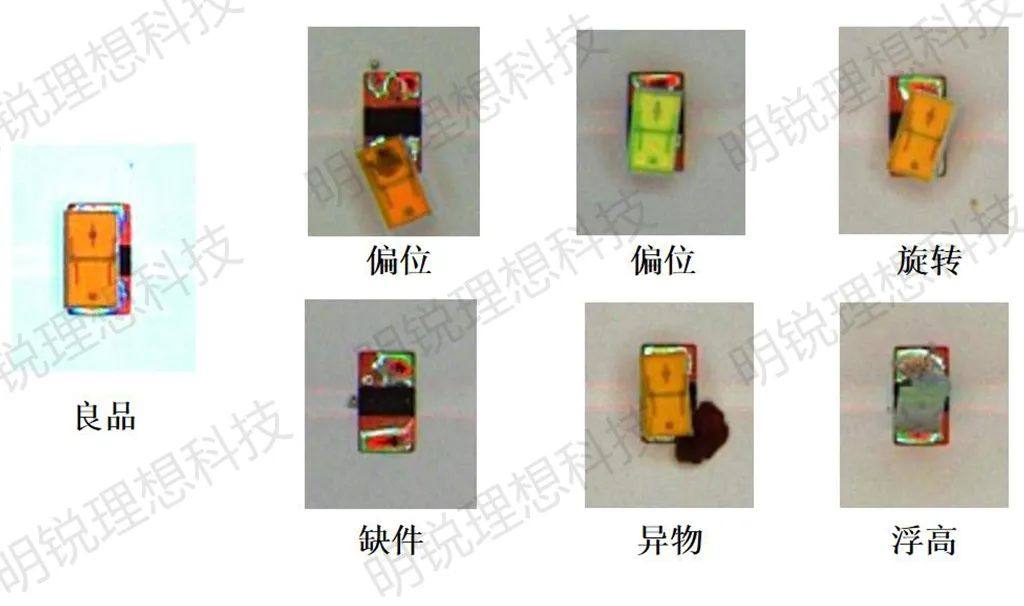
▼ 明锐AOI镜头下的Mini LED点胶后图像
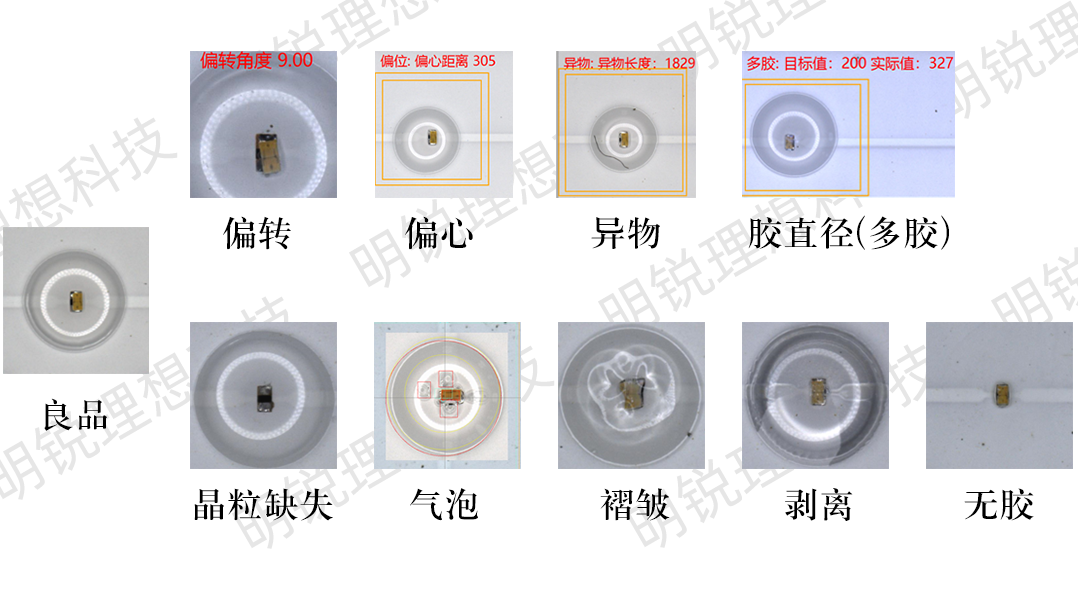
在Mini RGB直显产品检测中,通常会遇到几万甚至10万以上的芯片检测数量,因超大的计算量可能导致设备软件出现长时间的卡顿或者闪退,明锐AOI通过对软件程序读写、软件操作、检测算法等各方面的大幅优化,目前已做到了满足10万数量级芯片检测,未来将逐步满足20万数量级芯片的检测要求。
▼ 明锐AOI镜头下的Mini RGB直显炉前图像
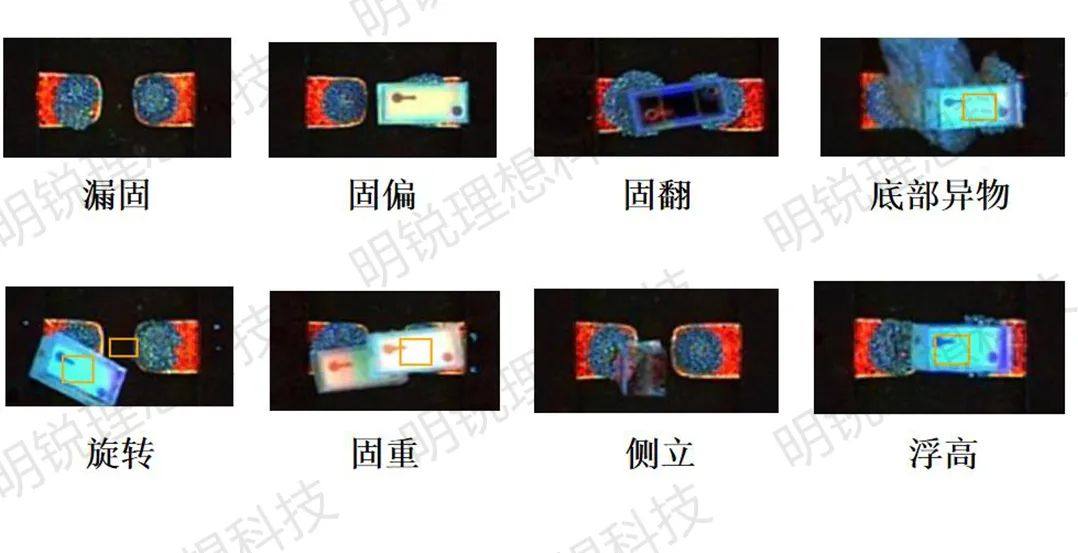
▼ 明锐AOI镜头下的Mini RGB直显炉后点亮图像
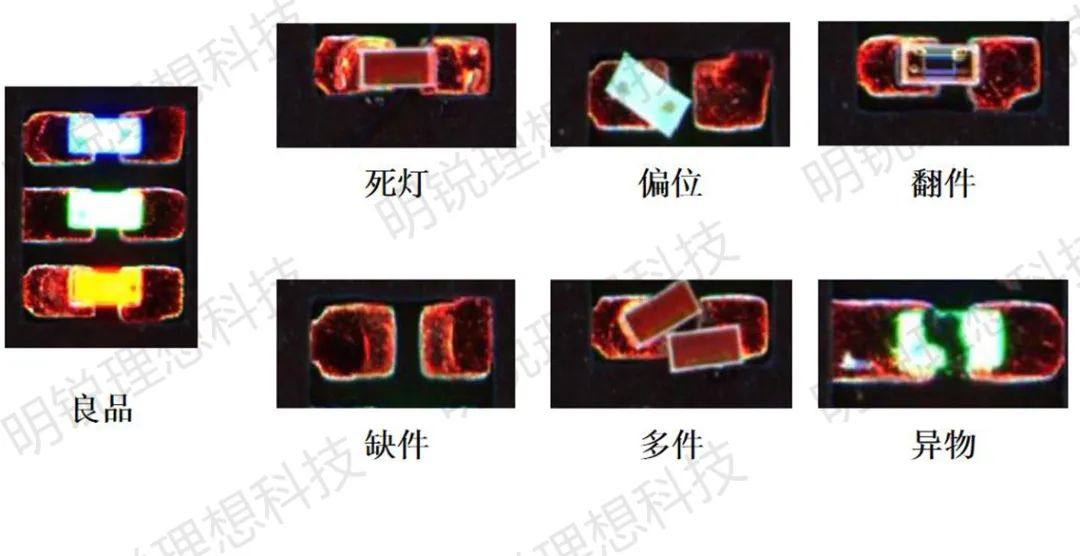
Mini LED背光在今年迎来了量产元年,尤其在电视背光领域已推出多款高阶Mini LED背光液晶电视。电视背光板尺寸大(500*300mm或更大),单片检测时间要求在60s以内(甚至40s),明锐AOI通过提高FOV拍照速度,优化软件计算速度,优化光学及传动等手段,为势必进入主流的Mini LED市场,时刻准备着最优的工业视觉检查方案。
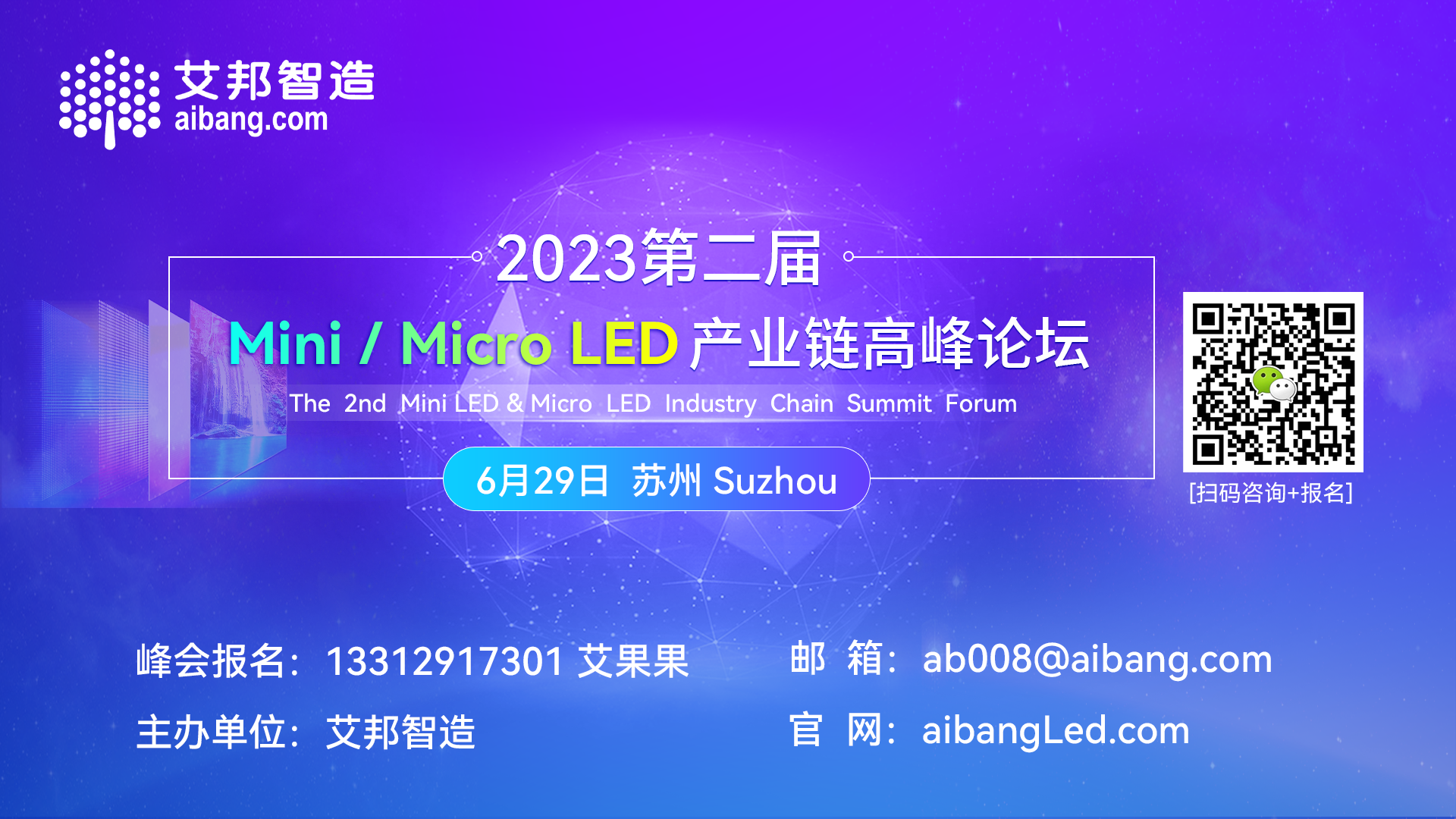
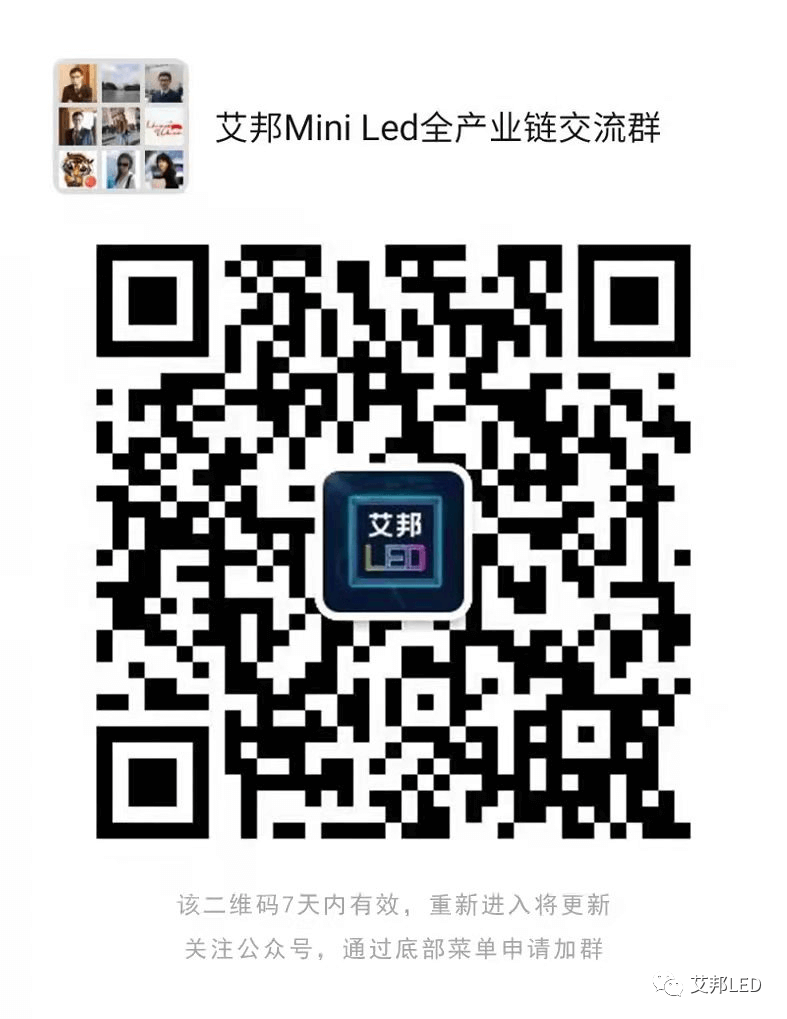
资料下载: